Buildings are highly vulnerable to the exposure of water, chemicals, and pollutants. This is due to the porous construction materials used to fabricate buildings. Over time, exposure to these elements will permeate your structure layer by layer, causing it to deteriorate and subsequently decrease its value. Through the use of certified waterproofing and sealing techniques, Our company will provide a barrier that will protect your building and ensure it remains structurally sound.
Waterproofing buildings is the method of forming a barrier over surfaces of foundations, roofs, walls and other structural members of buildings to prevent water penetrations through these surfaces. In summary, building surfaces are made water-resistant and waterproof.
Waterproofing can protect your building from leaks, foundation damage, deterioration, and more. It’s an ideal choice for commercial buildings, regardless of age or size. In this guide, we’ll discuss the basic waterproofing procedure and how it prevents water infiltration.
DIFFERENT TYPES OF WATERPROOFING PROCEDURES
Waterproofing is not a one-size-fits-all process. There are several waterproofing methods that can be used on their own or in combination with one another. Common waterproofing procedures include:
- Liquid waterproofing: where layers of liquid are sprayed or painted onto the surface. The layers harden to form a thick, custom-fit membrane.
- Cementitious waterproofing: where a special formula of cement is painted or skim coated onto the surface. The cement is not flexible like other waterproofing materials, so it is best used in areas that experience minimal shifting throughout the year.
- Bituminous waterproofing: available in membrane and liquid applications. This is a common alternative to liquid waterproofing because the bituminous materials adhere better to certain construction materials.
- Polyurethane membrane waterproofing: involves a heavy-duty membrane that stays flexible even after weather exposure. Other materials get brittle from UV rays, but the poly is incredibly durable. The only drawback to this waterproofing procedure is the heftier price tag.
COMMON STEPS IN COMMERCIAL WATERPROOFING
Every waterproofing solution is slightly different, but most involve the use of a membrane or liquid coating. The material is designed to adhere to the concrete/masonry on the building while remaining flexible enough to expand and contract with the seasons.
Your waterproofing procedure will likely consist of a consultation to determine which type of waterproofing is right for your building. From there, workers may excavate part of the ground around the building to access the foundation, unless it is already exposed. They’ll prepare the surface, apply the coating(s), and let the materials cure. Then, they’ll replace the excavated materials and clean the area.
In the case of interior waterproofing, the application is relatively similar, but there is no excavation required. Reach out to our company to start your waterproofing journey.
Steps involved in waterproofing process
Waterproofing Materials
waterproofing materials typically consist of a liquid polymer, such as polyurethane, acrylic, or bitumen-based compounds. These materials are specially formulated to provide excellent adhesion, flexibility, and resistance to water penetration.
Surface Preparation
Before applying the liquid waterproofing material, the surface needs to be prepared properly. This typically involves cleaning the surface to remove any dirt, debris, or loose particles. It may also involve repairing any cracks, holes, or damaged areas to ensure a smooth and even surface.
Priming
In some cases, a primer may be applied to the surface before the liquid waterproofing material. The primer enhances adhesion between the substrate and the waterproofing material, ensuring a strong bond and improved performance
Application
The liquid waterproofing material is applied to the prepared surface using various techniques, such as brushing, rolling, or spraying. The material is spread evenly to achieve a uniform thickness and coverage. Multiple coats may be required depending on the specific product and application requirements
Curing and Setting
Once applied, the liquid waterproofing material undergoes a curing process to transform into a solid and fully waterproof membrane. The curing time can vary depending on the material and environmental conditions. During this stage, it is crucial to protect the freshly applied membrane from damage, moisture, and foot traffic.
Protection and Finish
After the liquid applied waterproofing membrane has cured, additional protective layers may be added, such as a topcoat or protective coating. These layers provide additional durability, UV resistance, and aesthetic finishes. The choice of protective coating depends on the specific application and desired performance characteristics.
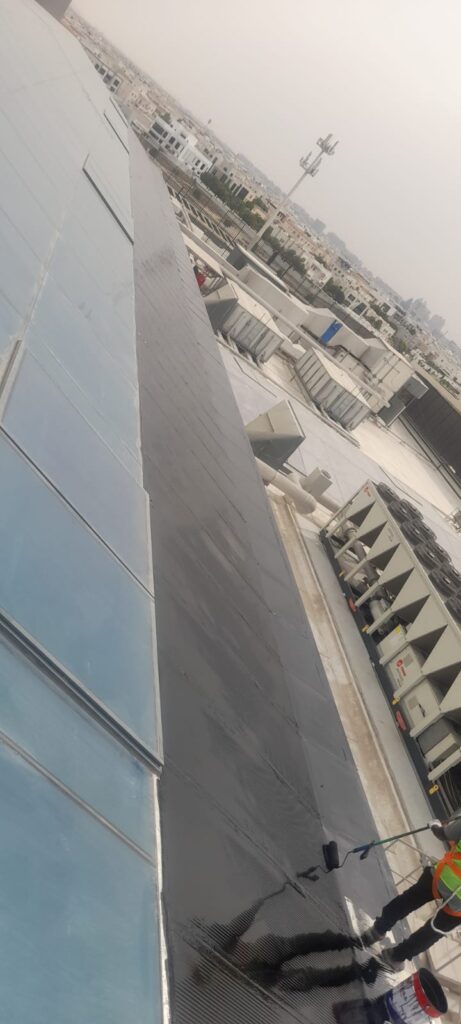
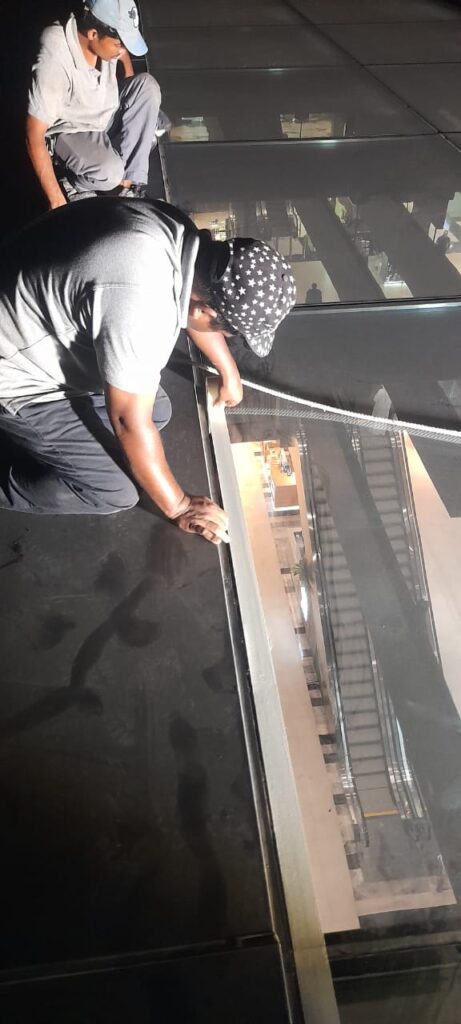
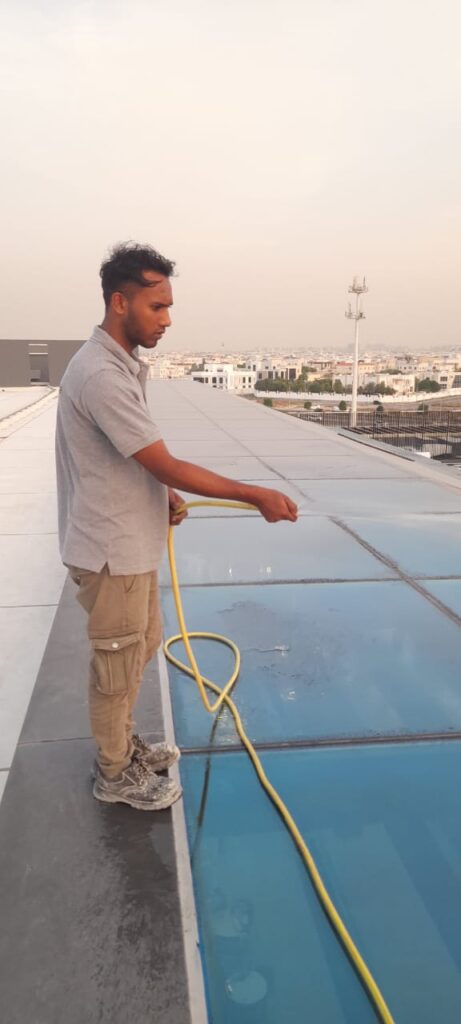